Unlike your weekend home improvement project, repairs in space require a lot of planning. It often takes months to come up with a workable plan that is safe, practical and effective. Contact Crawl Space Repair Bismarck for professional help.
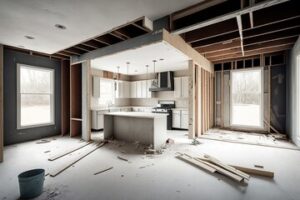
For example, the aforementioned goo gun required spacewalkers already clad in cumbersomespacesuits to strap on a tank that mixed heated red goo before being squirted out of a rifle-like nozzle. It proved difficult to apply and bubbled when mixed.
A spacewalk, formally called extravehicular activity (EVA), is one of the most significant milestones in human exploration. Since the dawn of space programs, astronauts have stepped outside their vessels for a multitude of reasons, including repair work and scientific research.
The average EVA lasts about six-and-a-half hours, and while the experience is incredibly rewarding for the crew members who perform them, it can be dangerous as well. This is because astronauts don’t have gravity to hold them in place when they are working out in space. This means that every movement they make requires a great deal of effort, and the risk for injuries is high.
In order to keep astronauts safe, countless hours of training and preparation precede every EVA. Astronauts learn to maneuver in their suits, familiarize themselves with the tools they will need and practice how to use them on the ground before flying to space. In addition, the astronauts and ground control teams build relationships and develop a dance that they can follow during each mission.
EVAs are not just used to repair space station components, but also to help maintain the orbiter itself. For instance, a small gash was discovered on the outer layer of the space shuttle Endeavour’s thermal tiles. This type of damage can cause the shuttle to lose heat and eventually break down. To fix it, NASA crewmembers drew on their experience from previous spacewalks to come up with an impromptu solution.
During a spacewalk on November 3, astronauts Piers Sellers and Mike Fossum used a tool that allows the crew to inspect thermal tiles from the inside of the spacecraft. In the process, they found a second tear in one of the thermal tiles. While this was a relatively minor issue, it prompted them to reschedule the rest of their EVA and work on a new technique that could prevent future repairs.
To test their plan, the astronauts will use a special paint to “wash” over some of the damaged thermal tiles with a material that can replace their eroded coating and improve the shuttle’s ability to reject heat during re-entry. It is hoped that this will help to avoid the kind of catastrophic damage that led to the loss of Columbia in two years ago.
Spacesuits
Spacesuits are vital for astronauts going outside of the International Space Station to perform extravehicular activity (EVA). They need to be able to protect them from extreme temperatures — they can be as hot as 250 degrees Fahrenheit in sunlight and as cold as minus 250 degrees Fahrenheit in shadow – while also providing the mobility needed to repair things around the space station.
EVAs are dangerous because they expose astronauts to the elements of space, including micrometeoroids and orbital debris moving at up to 70 kilometers per second. Occasionally these can cause puncture damage to a spacesuit. But more often, a spacesuit can leak or lose air rapidly because of wear or physical hazards like sharp tools or handrails. In fact, a spacewalking astronaut once nearly drowned because of a suit puncture that caused his helmet to fill with water.
A new type of spacesuit could help prevent such accidents. The new design is made from a special layer of material that is crisscrossed with current-carrying wires. So if the layer is punctured, built-in sensors will detect this and alert the astronaut. The new material is also self-healing.
In experiments, the material heals itself by oozing into any hole to plug it. This works because the inner layer is filled with a rubber-like gel sandwiched between two thin layers of polyurethane. In tests, the gel healed punctures up to 2 millimeters wide. The company that designed the material, ILC Dover, is already working with NASA to incorporate it into the next-generation of spacesuits for EVAs and lunar landing missions.
While this material won’t solve all of the problems with spacesuits, it may provide an important step forward. NASA is currently in the process of acquiring a number of next-generation spacesuits for its upcoming missions, including those to the moon and Mars.
The suits have to be lighter, more comfortable and better suited for the types of activities astronauts will need to do on those missions. The current EMU spacesuits, which were used during the Space Shuttle program, are getting a little worn and need to be replaced.
Thermal Tiles
Since a piece of foam insulation from the space shuttle’s external fuel tank broke off during liftoff and smashed through a tile on the leading edge of the orbiter’s left wing, NASA has been worried about the possibility of more tiles getting dinged. A hole in a heat-resistant tile would allow the searing hot gases of reentry to rush into the wing and cause catastrophic failure.
The wing is covered with thermal protective tiles and reinforced carbon-carbon (RCC) panels. In the past, scientists at NASA’s Ames Research Center proposed equipping a shuttle with a tile repair kit that could be used in orbit to patch up damage, but NASA managers did not pursue it. They also opted not to develop an inspection system so that astronauts could survey the tiles for damage.
But the shuttle’s reentry breakup has rekindled the idea of providing a tile repair option for astronauts to use in case they ever find a problem. And NASA is experimenting with one solution — a goo that astronauts can apply to a tile with something like a caulking gun.
The goo is a mixture of silica, alumina-borosilicate and aluminium oxide, all of which are found in the heat resistant tiles that make up a shuttle’s outer skin. The orange gel resembles cake icing and is designed to fill in a small hole or chip in a thermal protection tile. Engineers hope it will work in the same way as a conventional bonding agent.
If the goo does not hold up, NASA will try a more permanent fix with a squirt of adhesive similar to what a commercial rocket company uses for its Starship spacecraft. SpaceX officials say the goo and adhesive will help their spacecraft withstand the high temperatures of reentry.
Although a squirt of adhesive will probably not have the same effect as an actual repair, it will give engineers more data on how the tiles react under weightless conditions. That data may also provide clues on how to improve the tiles’ performance and durability, which is not an easy task.
Wing Leading Edge
For a long time now, engineers have sought to devise an in-flight repair system for the shuttle’s carbon composite nose cap and wing leading edge panels. These are different from the tile material, feature complex curved surfaces and endure the most intense temperatures during re-entry.
Fortunately, a few rudimentary tile repair techniques have already been developed. And, at this point, NASA managers have selected two of them – a “plug” procedure for larger holes and one intended to fix cracks in the wing’s leading edge panels – to be demonstrated during the first post-Columbia spacewalk.
The plug procedure is based on an existing “cure-in-place” ablator compound that would be applied by a spacewalking astronaut using a sort of high-tech caulk gun. Engineers have already tested the technique in arc jet facilities that simulate re-entry conditions. However, a number of other tests will need to be performed to determine the compound’s vacuum cure times and temperature limits before it can actually be used in flight.
It will also be necessary to figure out how a spacewalker can anchor themselves in the weightlessness of orbit and apply the patch without causing the station arm-work platform combination to flex too much. And then there’s the question of how to shape or smooth the repaired structure, if needed.
A damaged wing leading edge can be a real problem because it creates an air stagnation line where the stream of air has to choose whether to go over the top or beneath the wing. This causes drag and slows the craft down. On the other hand, a blunt leading edge buffers extreme cutting through the air and makes it behave more like an inverted v than a blade, allowing it to flow smoothly through the atmosphere.
In the past, a sharp leading edge has been used to provide lift for aircraft. More recently, however, it’s been replaced by slats that are operated electronically or hydraulically to reduce drag and offer better control at lower speeds. Still, some pilots prefer a sharp edge to maintain a more traditional aerodynamic profile.